Tech Question:
I've been having some issues with ring and pinion failure in a Chrysler 8.25” differential that’s in a ‘98 Jeep Cherokee. The first set failed in about 4,000 miles and the set that’s currently in it is on its way out as well. I'm by no means a Diff Wizard, but I have setup many with no failures until this particular case. After the first set failed I just bought a replacement and chalked it up to me overlooking something. That being said, when I rebuilt the diff the second time I paid very close attention to the details to avoid any mistakes but ended up with the same results.
I have shown the gear set to a few colleagues that have setup more diffs than I have and no one seems to have a good answer why it happened the first time, much less twice. When the first set started to howl or whine I pulled the cover thinking it was a pinion bearing going bad only to find the gears had worn enough that the backlash was out to .060 inches. None of the teeth were damaged on either the ring or pinion but all were worn down substantially. When it happened again, I removed the cover to find the same result, although not as worn as I caught it sooner. Backlash on the set that’s still installed is out to .035 inches currently. The locking tabs are still in place as they’re supposed to be. I checked them to make sure the adjusters hadn't backed off allowing the extra backlash. Both times the pinion bearing preload was still within spec. I also checked to see if I had failed to get a race fully seated but they were fine.
Any help or info would be greatly appreciated!
Thanks,
R. H. - Indiana
Tech Answer:
Examining your pictures, it looks like the initial setup is acceptable and not likely the cause of the issues you are having. The break-in process may be the culprit here.
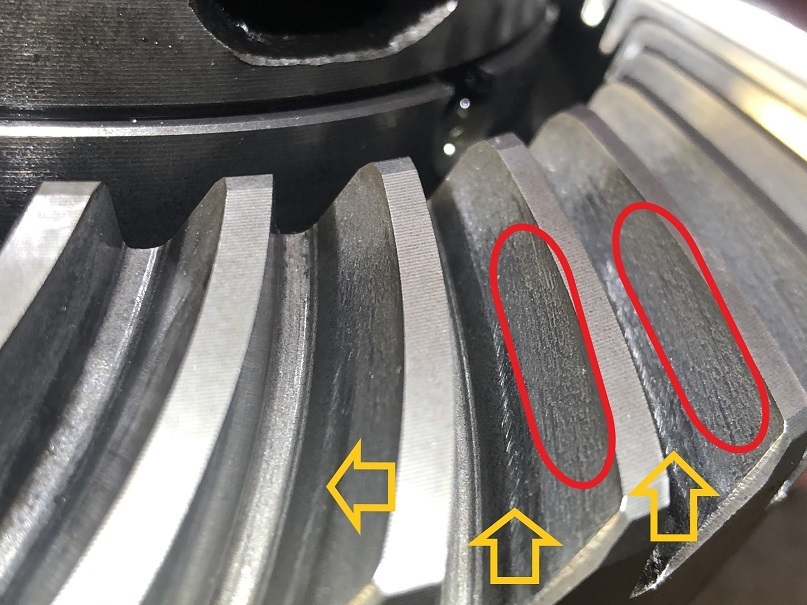
There are a few things happening. The first and most obvious, is gear meshing. During a proper break-in process as the temperature rises and pressure is applied, these forces harden and compress the grain structure by lapping or polishing the gear teeth surfaces. This creates a nice smooth surface for the teeth to glide across with minimal friction. If you look at the images of yours, they are still very coarse and have an exposed grain structure.
Another variable that is often overlooked is how, during the cool down process, the oil “quenches” the gears. This is just like in knife-making where the metal is super-heated then cooled in an oil bath. This process slightly changes the metallurgy on the surface of the gear face, transferring carbon etc. because we don’t want the gears glowing hot like in the manufacturing of knives. This heating and cooling cycle is repeated over and over in the drive cycles during gear break-in.
Properly breaking in deep gears on a small diff can be tough. The contact area is reduced, there is less metal in the pinion head to work as a heatsink, etc. Combine these factors with a gear set that spins fast can be compared to drilling a hole in a piece of steel with too high of a drill speed. You generate more heat than what the oil can dissipate, the oil cooks and loses its ability to lubricate, and the bit burns… compromising the cutting edge on the bit.
Looking at the teeth on your gear set, this seems to be what is happening. The oil is likely breaking down due to highly elevated temps, losing its ability to both dissipate the heat and provide proper gear lubrication. Once the oil gets this hot, it never really recovers. Sure, it will cool down and provide some cooling and lubrication, but not at the levels it once did.
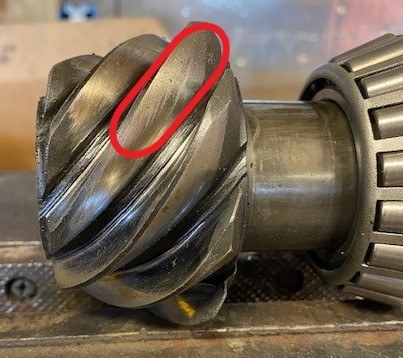
When internals get that hot during the break-in period gear meshing can also end up peeling the hard face that the initial break-in has built up. This is why your backlash changes. You have fractured and peeled off the hard face, exposed a rough grain structure, and taken the condition of the metal back to pre-break-in condition. Then you start the process all over again with even rougher gears… it’s a downward spiral. The problem is compounded because gear geometry has slightly changed as the teeth are thinner/smaller. Sure, you can reset the backlash to tighten it up and “fix” one of the variables, but it doesn’t address the real problem.
Another often overlooked issue is airflow cooling from under the vehicle. Running at highway speeds airflow on the diff actually becomes stagnant. It’s common to see gear sets burn not from actual overloading, but from driving too fast for too long and doing it too soon. Light throttle cruising at freeway speeds early in the break-in process, while seeming to be easy on parts, can generate more heat than the diff is able to dissipate. I find that this kills more gear sets than anything else during the break-in process.
My recommendations… Run a quality 80-90 GL5-rated conventional gear oil. Take it easy during the break-in process… short drives to get up to temp, let it cool to ambient temp, repeat. If you suspect that you might have gotten too hot, change the fluid, conventional gear oil is cheap. Remember, there is no filtration inside a diff, the only way to get wear particles out is to drain the diff, clean it, and refill. Conventional gear oil also has a slightly different carbon structure compared to synthetic oils and I find that conventional oil does a better job “quenching” the gear set. It also doesn’t seem to thin out as quickly and clings to parts better.
Gus Pyeatt, RANDYS Worldwide Tech Support
For more info on gear set break-in procedures check out this video.